Speed fasteners
High precision, system-compatible function, ease of operation and
quick processes are guaranteed because you can fasten continuously
from magazine or bowl fed fasteners and place up to 60 fasteners per
minute. For fast and reliable assembly processes.
Speed Fastening Systems can reduce assembly costs, shorten cycle times, increase productivity
and reduce rework and other quality costs. Speed Fastening Systems are well suited for use in
small, medium and large batch processes as well as continuous production lines.
Installation
For smaller batches, we offer a choice of power tools and simple assembly workstations. For
larger batches, multihead systems offer a cost effective solution. For continuous flow lines, we
have the technology to develop fully automated assembly systems.
Applications
Speed Fastening Systems can be used to assemble metal and plastics, composite material and
electronic components. With an average cycle time of less than two seconds, these systems
provide a fast installation from one side (blind).
Mission
Together with our customers, we develop blind fastening systems that simplify your
production process and improve the quality of your products. In every case, we not only see
ourselves as a provider of fasteners, tools and machines but as a development and system
partner with the objective of helping our customers improve their assembly performance.
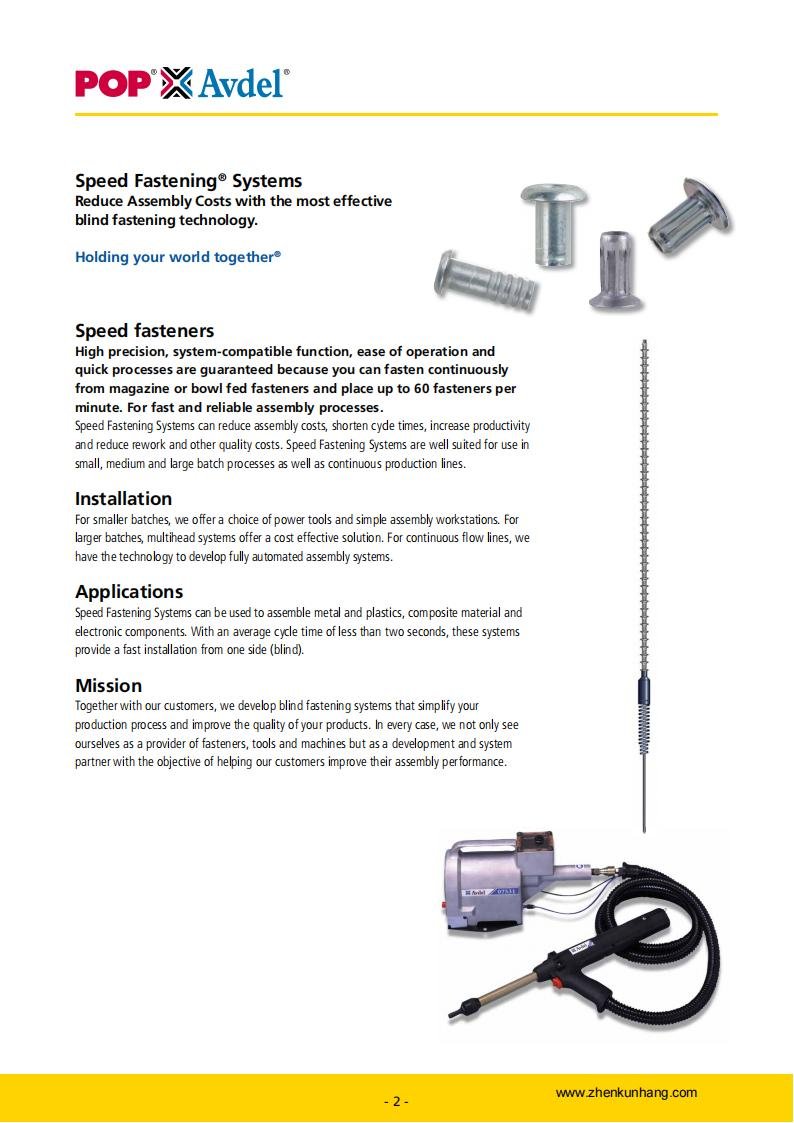
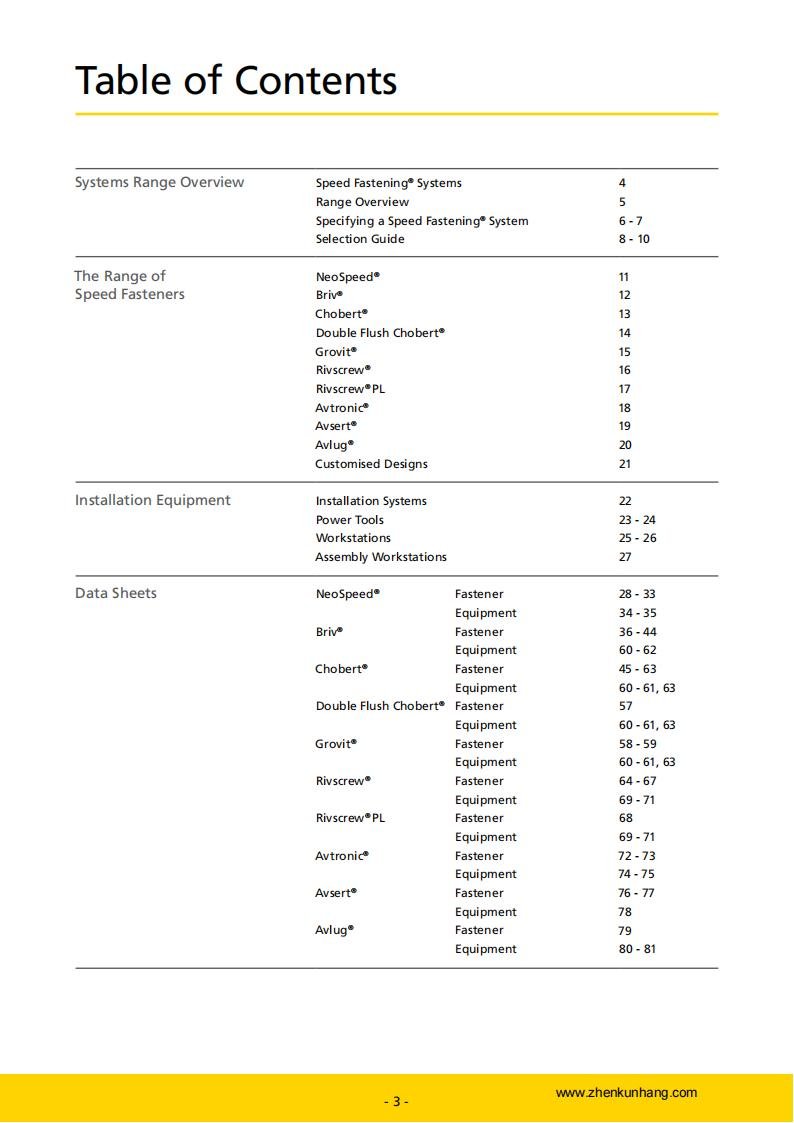
Speed Fastening is a unique assembly system designed for rapid and reliable fastening in medium and high volume applications. Originally designed for the aviation industry, Speed Fastening Systems are now used by many of the world’s foremost manufacturing companies in sectors as diverse as household goods, lighting,
electronic sub-assemblies, light metal fabrication and automotive. Speed fasteners are available in a wide range of materials, finishes, lengths and diameters and are ideal for fastening metals, plastics, composites and electronic components.
Speed fasteners are single piece fasteners which are either magazine fed or fed via a vibrating bowl to a wide choice of installation equipment. This ranges from the ultra-lightweight 753 power tool to fully automated, state of the art assembly systems.
Benefits of assembly
Increased manufacturing throughput
A Speed Fastening System can be fully optimised to give cycle times of less than two seconds. This rapid, blind sided process delivers a throughput up to four times greater than a traditional threaded or riveted solution.
Reduced component handling
The fasteners are fed via a magazine or into a bowl feeder. This eliminates the need for individual component handling, saves time and reduces the potential for operator injury.
No component spillage
Because the fasteners are captively held they will not be dropped onto the floor or into the application. This avoids wasted time and improves product quality while improving the work environment.
No stem loss
Traditional breakstem rivets all too often suffer from stem loss once installed. This can lead to application rattle, electrical short circuits or worse.
Speed fasteners have no stems.
Improved joint quality
Speed installation technology provides a consistent,repeatable joint. What’s more, unlike threadedfasteners, there is no requirement for torque control –no more problems of stripped holes or loose joints.
Improved joint performance
Once installed speed fasteners give excellent clamp up, shear and tension performance. They are also virtually immune from vibration loosening.
Process flexibility
Speed Fastening Systems can be used for low volume,off-line batch or jobbing shop work through to flowline processes. From hand held power tools to multi-
headed modular workstations, we can design a SpeedFastening System to suit your assembly requirements.A wide variety of products in many industries are
assembled with these systems including automotive,electronics, domestic appliance and general industrial.
Powerful Brands. Breakthrough Solutions.
At STANLEY Engineered Fastening we believe in seeking ways to serve our customers better. We create the future by anticipating our customers needs. Through diversifying our product lines, creating unique assembly technologies and offering a breadth of service to meet the demands of industry worldwide, STANLEY Engineered Fastening provides technological solutions to over 100 different industries.
Avdel®
Avdel has been producing assembly systems since 1936 and offers a comprehensive range of fasteners and tooling.
Dodge®
With a focus on high-quality threaded inserts for plastics products, Dodge has been a leader in the fastening market since the 1950s.
Gripco®
Gripco has been providing quality nut and threaded assembled products since 1904.
Heli-Coil®
Based on a long history that began in the aerospace industry, Heli-Coil offers a vast range of high-quality thread inserts.
iForm®
iForm continues a proud heritage since 1969 and represents over 40 years of creative threaded fastener application engineering.
POP®
From 2mm micro rivets to 1/4 "structuralrivets, POP blind rivets meet the needs ofmultiple markets.
Spiralock®
Spiralock is a technologically superior fastening system ideally suited forthreaded joint applications subjectedto heavy shock and vibration.
STANLEY Assembly Technologies
STANLEY Assembly Technologies supplies
production solutions to the global
assembly market.
Tucker®
A one-sided drawn-arc welding processis the foundation of the Tucker No-Holeassembly solution.
Warren® Whether it's plastic, metal, or acombination of the two, Warren candesign a product that will suit yourenvironment.
详情访问: 322-POPAvdel快速铆钉.pdf